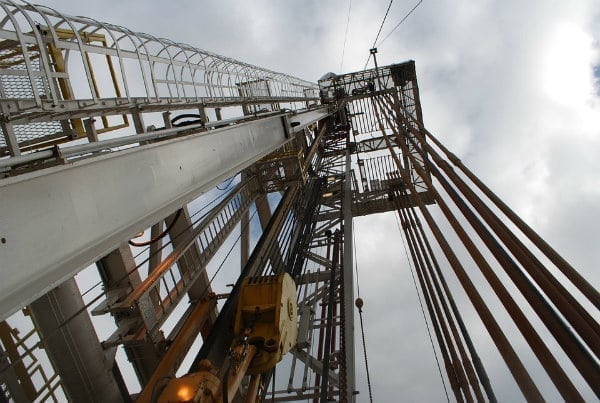
Without drills, there cannot be petroleum; without drill pipes, there cannot be drills. Drill pipes, as you know, play a huge, perhaps underestimated role in the drilling industry. These tempered, hollow steel pipes, hardened against accidents and to withstand the pressures inherent to subterranean conditions, pump drill fluid to the drill bit.
Because of the working conditions in which they operate, drill pipes generally have to be carefully checked and rechecked for wear and tear. To that end, they are assessed with spherometers, instruments which can precisely and quickly measure the radius of a sphere. After a spherometer check, drill pipes are classified in one of three categories:
- N-class pipe, or new pipe. The strongest, newest pipe available. Usually in pristine (or close to it) condition.
- P-class pipe, or premium pipe. A step down from N-class pipe, premium pipe have endured some wear, but can still function very capably.
- C-class pipe, of which there are three classes (C-1, C-2, and C-3). Depending on their rating, C-class pipes are either well-worn pipes, or nearing the end of their useful lives.
After a pipe has reached the end of its useful service life, they will be graded for scrap, denoted with the application of red bands. Because of the high cost of drill pipes, remember that they are often reused, with many companies selling both new and used pipes (graded according to the criteria mentioned above) often until the very end.
Now that the basics of drill pipes are covered, let’s take a look at the several types that are available.
- Drill string. The drill string refers to the entire column of tools, essentially the drill pipe, shaft collar, tools, and the drill bit itself. Generally, drill pipe used for the drill string is made from tempered steel. For cost and transport reasons, sections of drill pipe rarely exceed ranges of 30 to 33 feet long. As a result, given the extreme depths involved in drilling (particularly offshore), which can reach almost 15,000 feet, different sections are usually connected with tool joints; one section of pipe will have a male connection, which is then paired with a female connection.
-
- Note that drill pipes will have different thicknesses, which are specified. Examples include (but are not limited to) 2 ⅜ inch thick drill pipe, 5 inch thick drill pipe, and 6 ⅝ inch drill pipe.
-
- Drill pipes used in the upper parts of the drill string differ in both thickness and construction from heavyweight drill pipe (HWDP), used to transition between drill collars and regular, thinner drill pipe. HWDP will be discussed below.
- Heavy Weight Drill Pipe (HWDP). Heavy Weight Drill Pipes are, as mentioned before, much stronger than regular drill pipes, because they are designed to deal with the added pressures and stresses arising from serving as transitions between drill collars and regular, thinner drill pipe.
-
- Generally, HWDP are preferred for transitions because they are more flexible than alternative, solid connections.
-
- Note that such piping is thicker, ranging in diameter from 3.5 inches to 6 ⅝ inches, weight almost twice as much lb/ft as regular drill pipe, and is often rated with tensile strengths ranging from 200,000 lbs to over 1,000,000 lbs.
-
- Interestingly, drill pipes often are equipped with a center upset, or thick wear pads that prevent the outside of the drill pipe from grinding against the rough bedrock of the hole walls. Generally, center upsets are a desirable addition to heavy weight drill pipes, especially since by reducing wear, tear, and friction, they can prolong the lifespan of drill pipes.
With this in mind, remember that drill pipes, while they come in a variety of sizes, diameters, and materials, are divided into two broad types: regular drill pipe, and heavy weight drill pipe (HWDP), used as transitions. Generally, most pipe types can be bought new or used, and are graded according to three broad categories (New, or N; Premium, or P; and C, which has three subdivisions).