When most people think of drilling, they probably picture a large bit drilling into the earth. This should not be surprising, as rotary drilling is one of the most popular drilling methods used today. Nevertheless, rotary drilling has its limitations, and other methods are available. This article covers the basics of rotary drilling, and then discusses some common alternatives used today.
Rotary Drilling
Rotary drilling is a drilling method that uses a sharp rotational drill bit to drill into the earth. The most common drill bits used today include:
·Roller Cone Bit – Designed to crush hard formations.
·Drag Bit – Made of tungsten carbide and steel, this bit is used with softer formations such as soft rock and clay.
·Polycrystalline Diamond Bit – Made of diamond inserts attached to carbide inserts. 40 to 50 times stronger than standard bits, these are used to drill into the hardest formations, and are rapidly becoming as common as traditional bits.
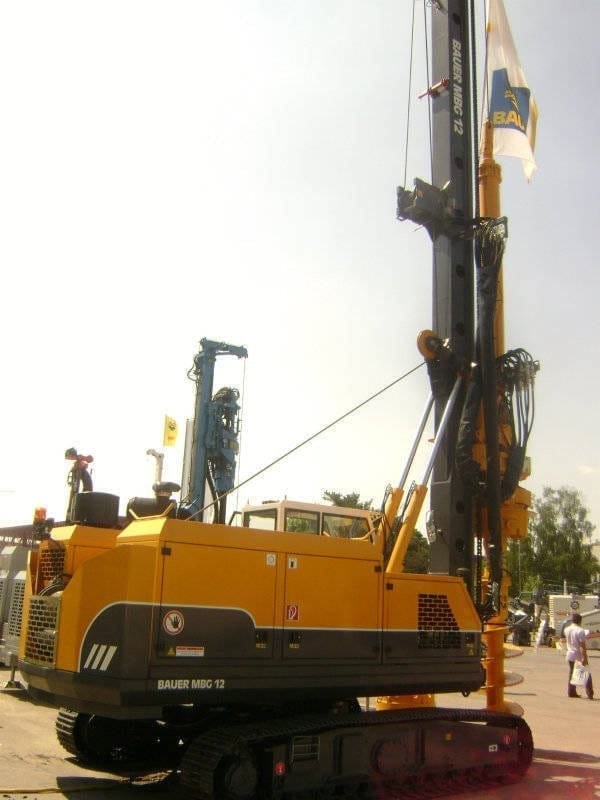
Rotary drilling rigs consist of the following components:
·Prime Mover (Power Source) – Diesel engines are the most common power source for rotary rigs. Other options include natural gas engines and reciprocating turbines.
·Hoisting Equipment – Tools used to lift and lower equipment into and out of the well. The derrick extends vertically from the drill hole and serves to support the cables and pulleys that lift the equipment in and out of the well.
·Rotating Equipment – Components that take the power provided from the prime mover and use it to rotate the drill bit. The swivel, attached to the hoisting equipment, supports the weight of the drill string, allowing the bit to rotate with minimal interruption.
·Circulation System – Used to cool and lubricate the drill bit, remove drill cuttings and debris and coat well walls. The system includes drilling fluids, drilling pumps, injectors and compressors.
Although rotary drilling is the most popular method, drilling samples can be inaccurate. This is because cuttings removed from the bit are exposed to loose formations further up the drill hole. These loose formations can be mixed with the cuttings, resulting in an inaccurate representation of the formations present at the drilled depth.
Alternatives to Rotary Drilling
Reverse Circulation (RC) Drilling
This technique uses a dual wall drill pipe made of an inner and outer tube. Air is injected down the rod, resulting in the lifting of water and cuttings up the inner tube. Drill cuttings are then brought to the surface inside the rod. The liquid and cuttings reach a deflector box at the top of the drill string, and then move through a sample hose connected to a cyclone. From there, the drill cuttings move through the cyclone until they fall through an opening at the bottom to be captured as a sample.
Air Drilling
This technique uses gases, typically compressed nitrogen or air to lift cuttings out of a well and keep the drill bit cool. Used in place of traditional drilling fluids, types of air drilling include:
·Mist Drilling – Air drilling incorporating the use of liquids such as water, soap and chemical inhibitors to create a mixture. This mixture is then included in the air steam to assist in hole cleaning.
·Foam Drilling – Technique in which air is combined with water and surfactants to create a replacement foam for traditional drilling fluids.
·Aerated Drilling – Technique in which air is added to drilling fluids, resulting in a lower density than traditional fluids alone.
·Nitrogen Membrane Drilling – Technique which offers several advantages including a lower risk of down-hole fires or explosions.