Slip-type tubing elevators hold and hoist tubing for completion and production operations.
They are especially suitable for the hoisting of integral joint tubing.
Keystone slip-type tubing elevators come in four types: the 20-ton “LYT”, 40-ton “MYT”, 75-ton “YT” and the 150-ton “HYT”. Tubular sizes are from 3/4” through 3 1/2”.
All slip backs and die slots on Keystone slips are precision machined to ensure proper grip and to prevent bottlenecking or slip cuts to the pipe. All Keystone slip type elevators are manufactured in the United States and built to meet or exceed API 8C standards.
Our slips and elevators come with a complete data book, including material and heat certification. This certification ensures your equipment is manufatured with steel from trusted vendors. The KET and API stamp indicate a seal of quality.
When ordering, please specify:
- What size inserts to be dressed with slip body
- Extra insert sizes
- Spare parts
LYT Slip Type Elevator
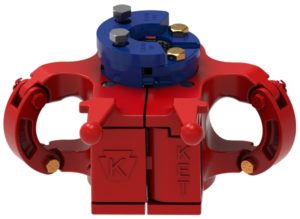
The LYT 20 Ton Slip Type Elevator is designed to handle small size tubing. The LYT size range is 3/4” through 2-1/16” and requires only one size slip to handle its full range. Rated capacity is 40 tons.
MYT Slip Type Elevator
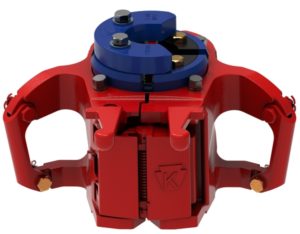
The MYT 40 Ton Slip Type Elevator is a lightweight tubing elevator used for holding and hoisting oilfield tubing. The MYT size range is 1.315” through 2-7/8” and requires only one size slip to handle its full range. Rated capacity is 40 tons.
YT Slip Type Elevator
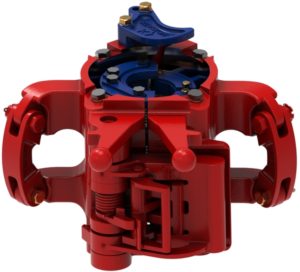
A medium weight tubing elevator for tubing 1″ through 3 1/2″, the YT requires the use of two sizes of slips to handle its full range. Rated capacity is 75 tons.
HYT Slip Type Elevator
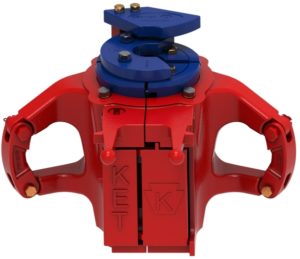
A heavyweight tubing elevator, the HYT is for tubing 2 3/8″ through 3 1/2.” It requires only one size of slips to handle its full range. Rated capacity is 150 tons.
Keystone also carries slip-type elevator parts, including rings, hinge pins, latch pins, cotter pins, latch locks, and slip bolts.
Safety Concerns with Rig Floor Equipment
When drilling operations call for the use of slip-type elevators, the following precautions should be taken:
- Slip-type elevators must close completely, and the latch must engage properly. Double-check the elevator body, latch mechanism, links, and dies and setting plate. Keep hands away from any pinch point or undesignated areas; use only the provided handles for operating the elevator.
- Elevators should be cleaned frequently to reduce the risk of slippage, and to ensure that they are working properly. If slips are used, make sure the dies are clean and sharp, and all of the same size. Do not mix old or resharpened dies with new dies in the elevator slips.
- Blocks should be completely stopped prior to latching the elevators on the pipe. The blocks must be raised slowly to allow the elevators to slide up to the pipe upset area. Check that the blocks are centered over the rotary table. Any misalignment can result in difficulty when stabbing and spinning up connections.
- Pipe should be stood back in the derrick no further than necessary, eliminating as much “bowing” as possible. Personnel responsible for “tailing” the pipe should keep the pipe at arm’s length at all times.
- Workers should never position themselves directly under stands or joints of the drilling string. Use a tail rope that allows employees to stand well away from the pipe at initial pick-up.